Zero waste
Not just a pipedream.
When you’re as passionate about sustainability as we are, you keep pushing the boundaries, pressing for change.
Using only recycled raw materials, eco-friendly production processes and a low-zero waste programme, we put the responsibility into luxury.
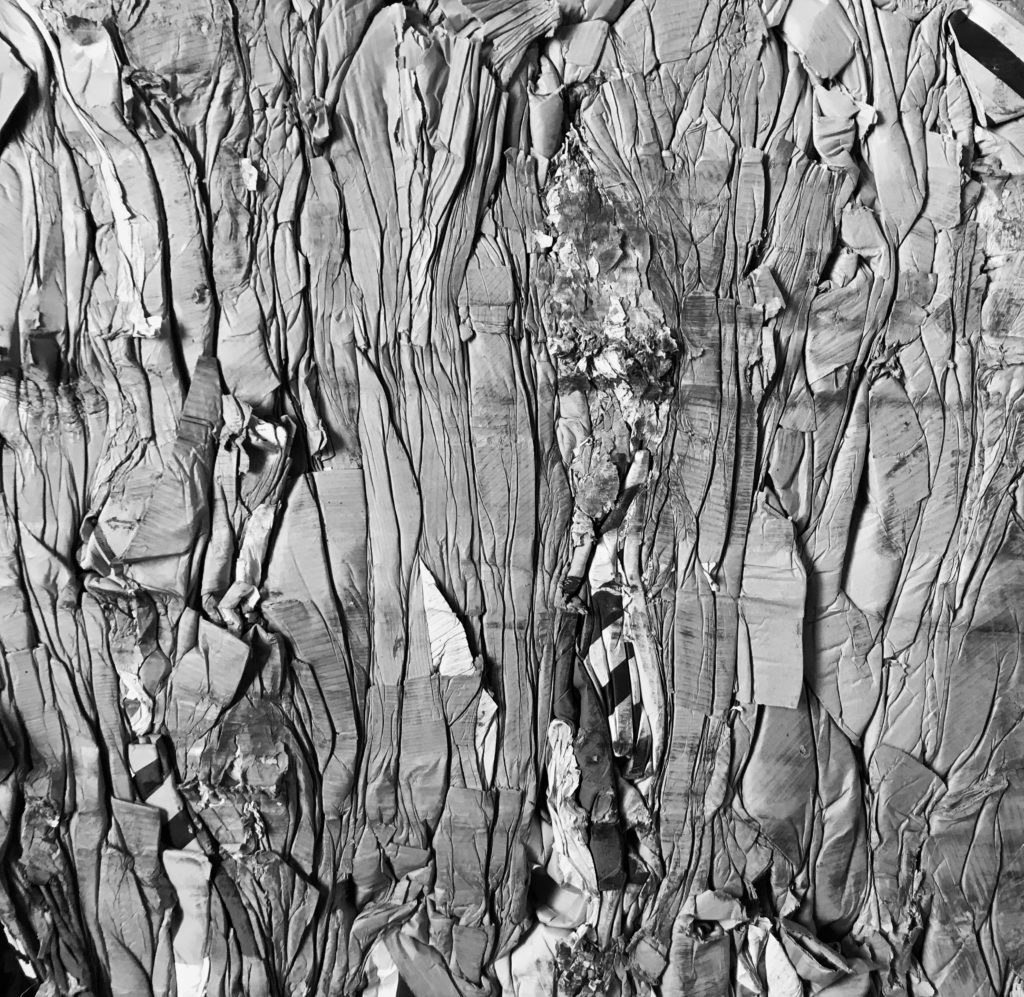
To be the best— we never rest
We are constantly creating, inspiring, innovating, engineering and pioneering our product, and we believe that anything is possible.
If they say it can’t be done, we simply set out to do it.
We work closely with our clients to inspire and excite them. There are always new ideas to explore, new concepts to create and new ways to ‘wow’.
Everyday we strive for the original, the beautiful, the sustainable solution.
From 100 to 0
With success, comes responsibility. It’s something we take very seriously. In fact, for over 100 years we’ve championed recycled paper, with a unique green production process and a zero-no waste goal.
This strict environmental ethos applies to our paper, our partnerships, and our planet alike.
No compromise. No short cuts. We stay true to who we are, from pure product to spearheading the brands of tomorrow; we have been architects of identity materials since 1879.
Working for zero waste for 140 years
It’s a sustainable cycle.
From raw materials to circular processes, the more energy we generate, the more sustainably we work.
Discover our processIn the sustainability— vanguard
We’re advocates of eco-energy, crusaders of sustainability and pioneers of new technology, production methods and facilities. We never stop in our quest to bring you the best.
Pure, and proud
We were among the first to move to using recycling paper as a raw material.
Nearly 95% of all our raw material is now recycled.
We were first to work with a virtually closed process water system – our water consumption fell to 1.8m3 water per tonne of end product.
Generating bio-gas from wastewater provides us with a heat source.
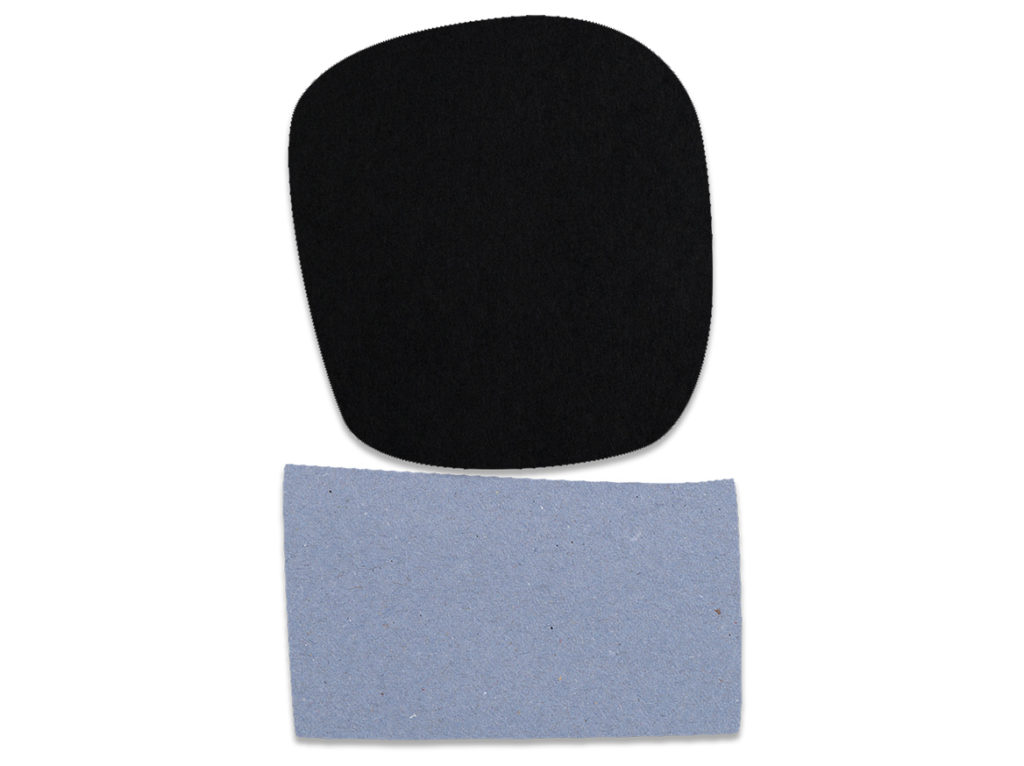
Setting and hitting the highest targets
Each year we set ourselves the task of improving the quality of our entire operations focusing on quality, health and safety, energy and environment.
We’ve been striving for ultimate sustainability for over 25 years and on average, have reduced our impact by 1% to 1.5% per year.
We never get complacent, proactively working with partners to set eco wheels in motion long before legislation even requires it.
Take our gasifier; with this technology alone we have seen a 30% decrease in energy use and a 75% reduction in waste!
RDM Sustainability Report 2023
On the Road to the Future
ESKA is part of RDM Group, the leading producer in the recycled cartonboard business and the largest producer in Italy, France, the Netherlands and in the Iberian Peninsula. While coated board is mainly supplied to the European market, solid board is representing a leading segment worldwide including US and Asia.
The Sustainability Report intends to accurately and transparently represent the results achieved by RDM Group in developing the business activities with a view to growth and creating value for all the stakeholders in the long term.
more about RDM![cover[1]](https://eska.com/wp-content/uploads/2022/08/cover1-724x1024.jpg)